BLADE BASICS 101
BLADE BASICS 101
A diamond blade is a circular steel disc with a diamond bearing edge. The blade edge comes in three main types: segmented, with individual separate segments for long life; turbo, with continuous serrated edge for aggressive, fast cutting; and continuous rim, for smooth chip-free cutting.
The core of the blade is made of tensioned steel and sometimes has slots. These slots (also called gullets) cool the blade by allowing water or air to flow between the segments. They also allow the core to flex and dissipate stress while cutting, so the blade is less likely to crack. All blades are designed to run at specific rpms. It’s essential for safe operation and optimum performance that blades run at the correct rpm.
The diamond edge is made of a combination of manufactured diamonds and metal powders. Different mixtures of diamonds and metal powders are used, depending on the aggregate being cut. During the manufacturing process, the metal powder and diamonds are bonded together at high temperatures to form a solid metal alloy. This metal alloy is then bonded to the blade. A blade’s diamond edge is always slightly wider than the core so it doesn’t drag or bind in the material being cut.
A diamond blade cuts by grinding through the material. As the diamond edge wears, new and sharper diamonds are exposed.
CHOOSING THE RIGHT BLADE
Answer these simple questions when choosing your blade, or ask your World Diamond Source representative for advice.
- 1. What type of material is being cut?
- 2. Do you want a segmented, turbo or continuous rim blade?
- 3. What is the diameter of the blade?
- 4. Does the rpm of the saw, based on blade diameter, fall within the guidelines?
- 5. Will the blade be used in a wet cutting or dry cutting application?
- 6. Are you more concerned with the initial price or cost effectiveness of blade?
WET BLADES
Wet diamond blades must be used with a continuous flow of water to maximize performance and prevent excessive heat buildup. Water helps clear dust and cuttings away from the blade and slot being cut. Using a wet blade without adequate water, even for a few seconds, can cause blade damage and pose a safety hazard.
DRY BLADES
Dry diamond blades are designed to be cooled by airflow around the blade. They can be used either dry or wet. Note that every 10 to 15 seconds it’s necessary to take pressure off the blade and back it out of the cut, allowing it to run back up to full speed for several seconds. This technique cools the blade, maximizes performance and prevents excessive heat buildup that causes damage.PRODUCT WARRANTY
World Diamond Source warrants all its products against defects in workmanship and materials for a period of one year from the date of purchase. The responsibility of World Diamond Source under this warranty is limited to replacement or repair of the defective parts, and action will be determined on a case-by-case basis. Under no circumstances will World Diamond Source be liable for consequential or incidental damages arising from misuse or improper operation of any products.SHIPPING POLICY
World Diamond Source pre-pays freight on all orders via United Parcel Service or FedEx – Ground within the United States and Canada. Special service requests, such as next-day air or second-day air, is payable by the customer.AGGREGATE CLASSIFICATION MAP OF THE UNITED STATES
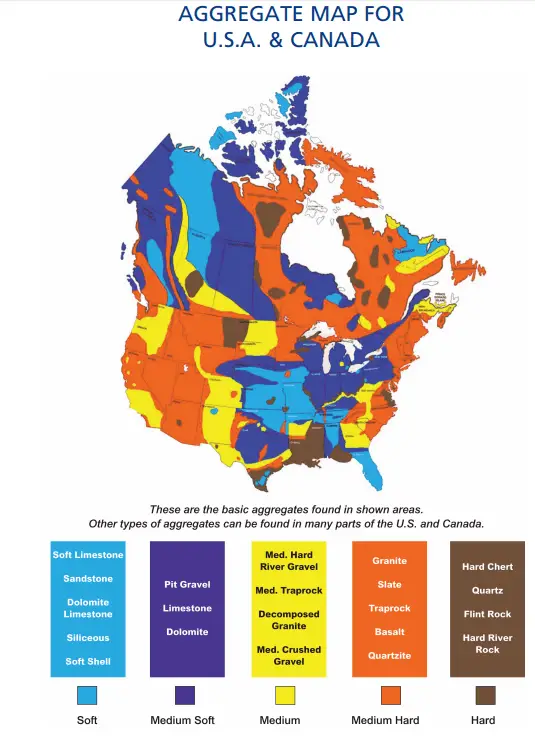
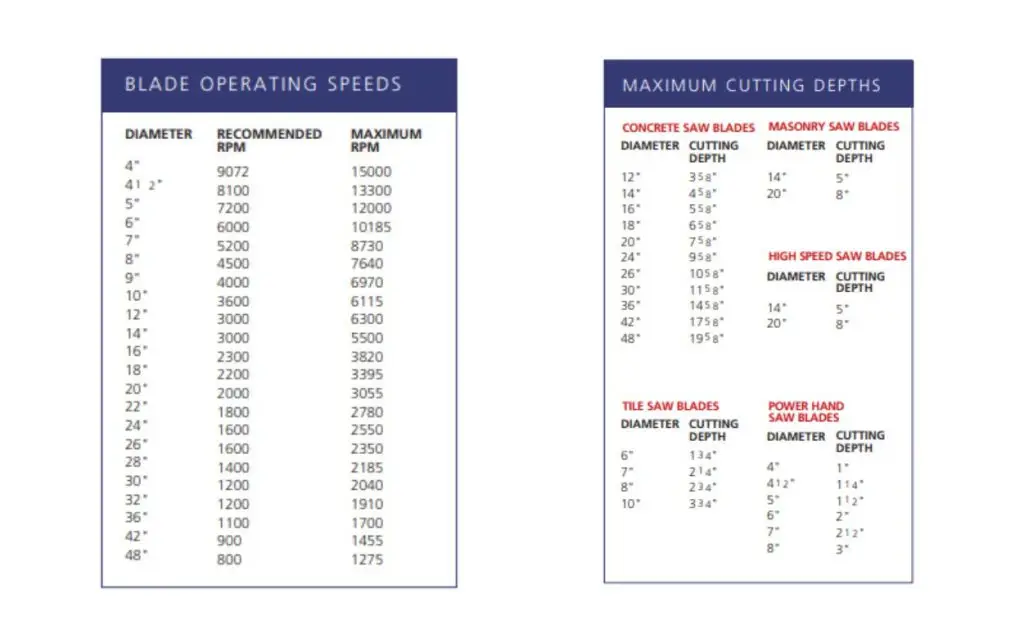
HOW DIAMONDS ARE MADE
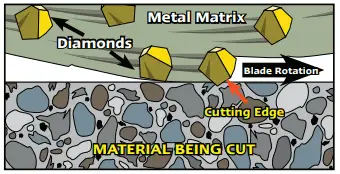
The exposed diamond crystals do the grinding work. The metal matrix or bond holds the diamond in place. Trailing behind each exposed diamond is a bond tail which helps to support the diamond. As the blade rotates through the material, the exposed surface diamonds grind the material.
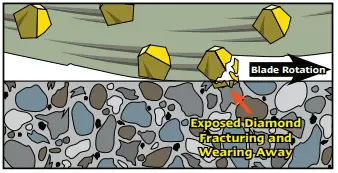
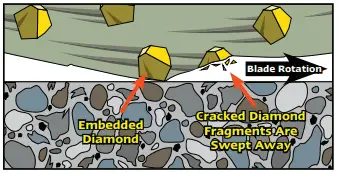
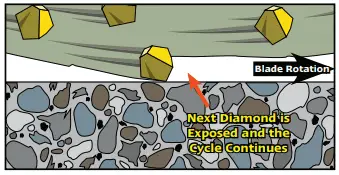
#1 RULE FOR DIAMOND BLADES: USE A HARD BOND TO CUT SOMETHING SOFT AND USE A SOFT BOND TO CUT SOMETHING HARD DIAMOND QUALITY - YOU GET WHAT YOU PAY FOR
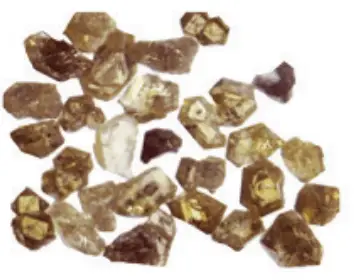
LOW QUALITY
SYNTHETIC DIAMONDS
- Weaker crystals with irregular shape
- Shorter life & lower cutting rates
- Lower thermal stability
- Does not handle steel & hard aggregates well
- Jagged points that break causing faster wear & lower cutting & drilling performance
- Widely used in low priced dry products
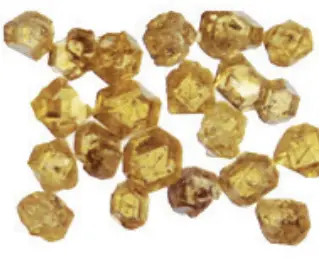
MEDIUM QUALITY
SYNTHETIC DIAMONDS
- Good crystal strength & shape
- Good for sawing & drilling applications
- Good cutting speed
- Handles moderate steel & hard aggregate applications
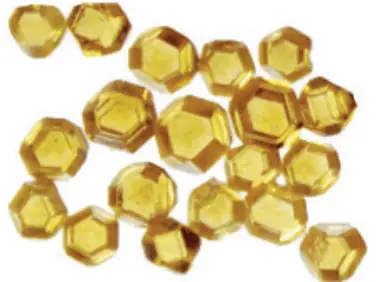
HIGH QUALITY
SYNTHETIC DIAMONDS
- Strongest crystals
- Lasts longer
- Withstands high temperatures
- Octahedral shape for increased tool
- Life & faster cutting
- High impact strength against steel &
- Hard aggregate